系统智能化认知
研究成果1:数字孪生建模方法
- 所有制造资源都有模型,从工具到设备、从制造系统到工厂,一切都是模型
- 全寿命模型,从材料到产品,从产品(包含零部件)构思、设计、开发、制造、出厂、使用到报废,构建覆盖产品全寿命的可持续演化的数字样机。所有模型根据他们的作用关系和历史沿革完美的融合在一起。模型是活的,就像生命体一样可以述说他们的过去、现在和未来。
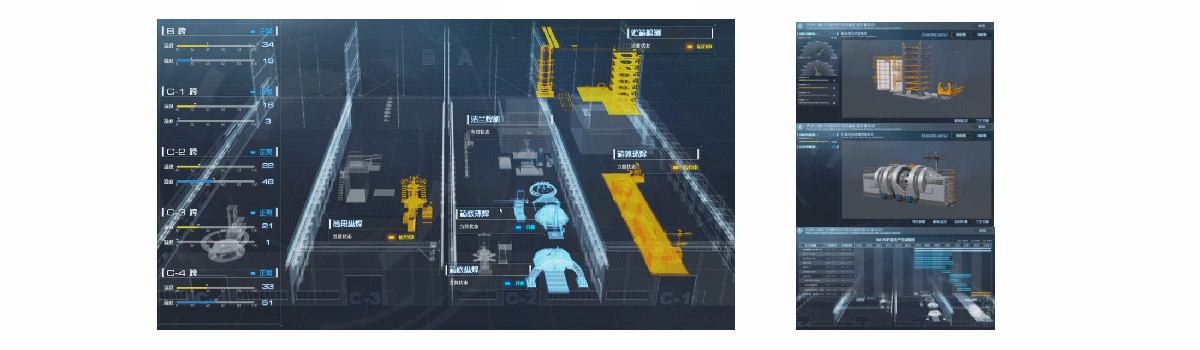
研究成果2:生产线数字孪生监控系统
在数字孪生模型的构建、数字孪生模型的动态组合以及虚实信息同步等技术的基础上,对车间中的人机料环进行数字孪生模型构建,通过区域模型的的动态映射机制,实现车间的可视化以及生产要素状态的同步展示。同时,根据全息车间中产品加工产线的实现逻辑图、设备三维模型、现场设备动作同步进行;生产线的工艺工序与逻辑图一一对应,逻辑图按照实际生产工序进行同步跟踪,实现对零件加工过程中产线运行情况的实时把握。
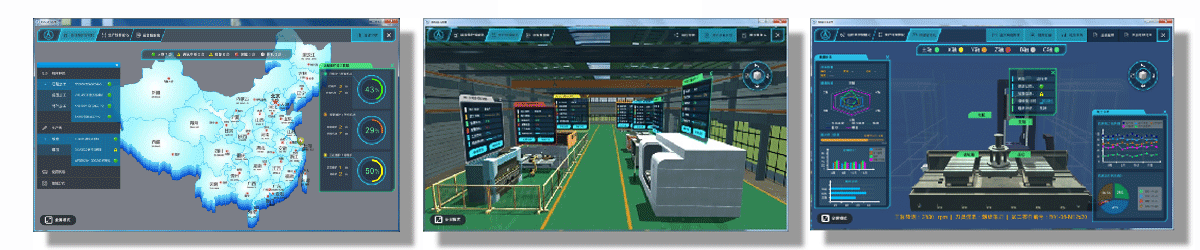
数字全息模型为载体,在对系统运行状态、加工状态实时感知的基础上,用于实时工况与系统能力、健康状态的实时监控、分析与预测。多终端APPS可将所有运行数据在PC、手机、平板等终端进行实时展现,支持Windows、Android、IOS系统。
该系统已经在航天某厂进行应用
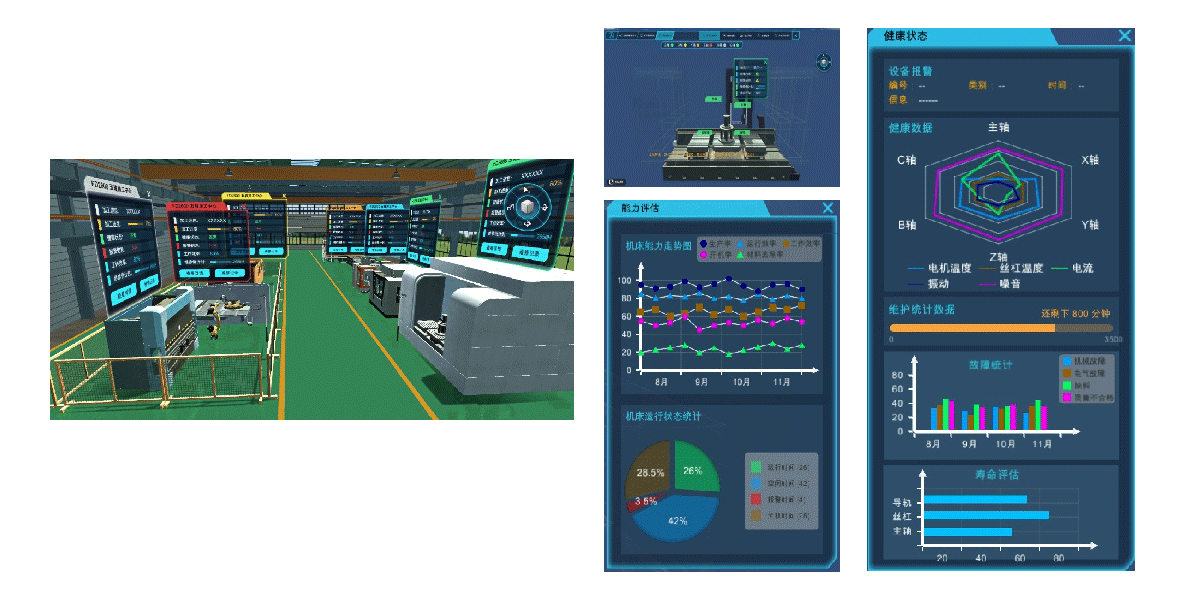
研究成果3:基于数字孪生的深度学习可计算系统
针对生产系统的认知需求,结合数字孪生建模技术与深度学习技术,研发基于数字孪生的深度学习可计算系统,以研发的感知技术、计算技术和认知技术为基础,提供大数据分析处理的能力,结合数字孪生技术进行可视化展示,实现不可见要素的可视化。
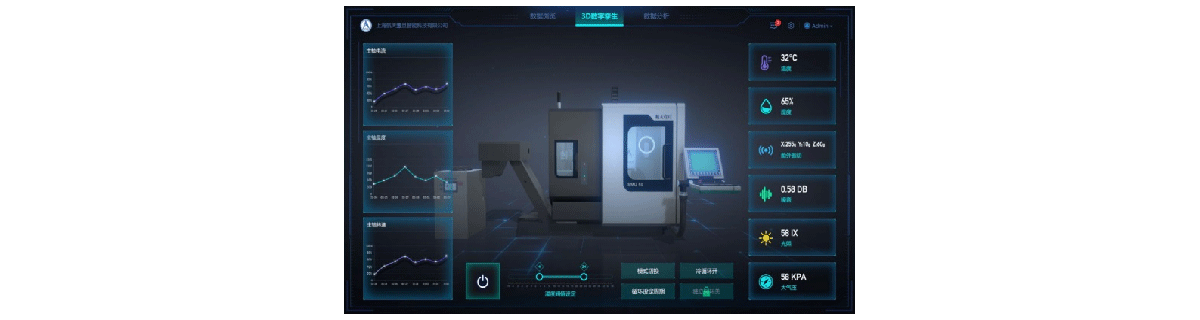
研究成果4:基于MachingGPT的智能制造平台
本团队自主研究的基于MachingGPT的智能制造平台,GPT引擎根据其内置算法,获取边缘端获取处理后的实时数据,切实解决工程实际问题。
GPT引擎:
- “体检”:加工过程实时监测
- “诊断”:预判与评估
- “诊断”:基于Bert模型的工程问题的影响因素和影响状态分析诊断
- “治疗”:基于GAN模型的自主生成式工艺优化
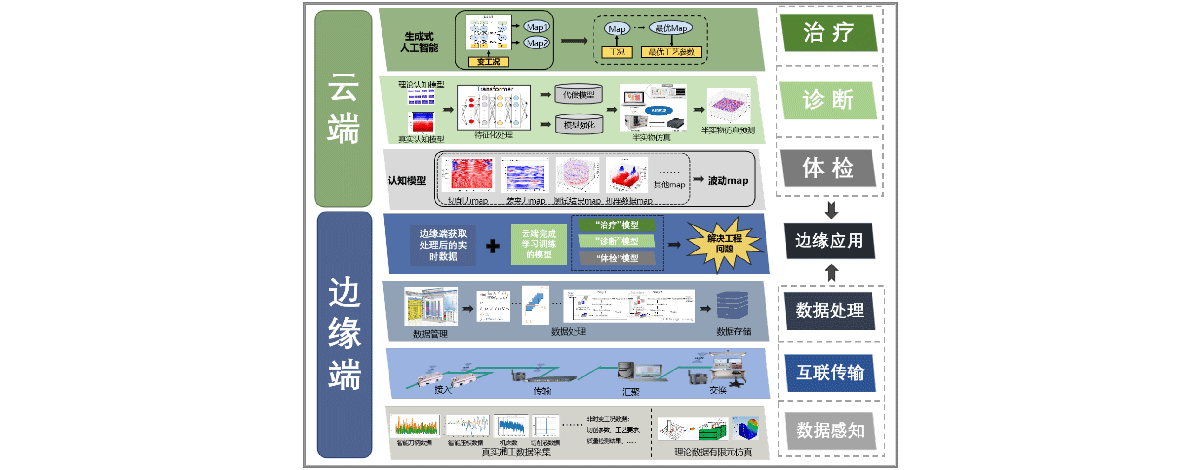
研究成果5:叶片装配中不平衡量半实物仿真预测模型
二级盘模拟件叶片装配,叶片数目32,在安装编号为16的叶片时错装为12号,通过半实物仿真模型预测出最终的不平衡量为549.2 g.cm,超差,根据预测结果对后续叶片排布方案进行优化,降低为17.71.
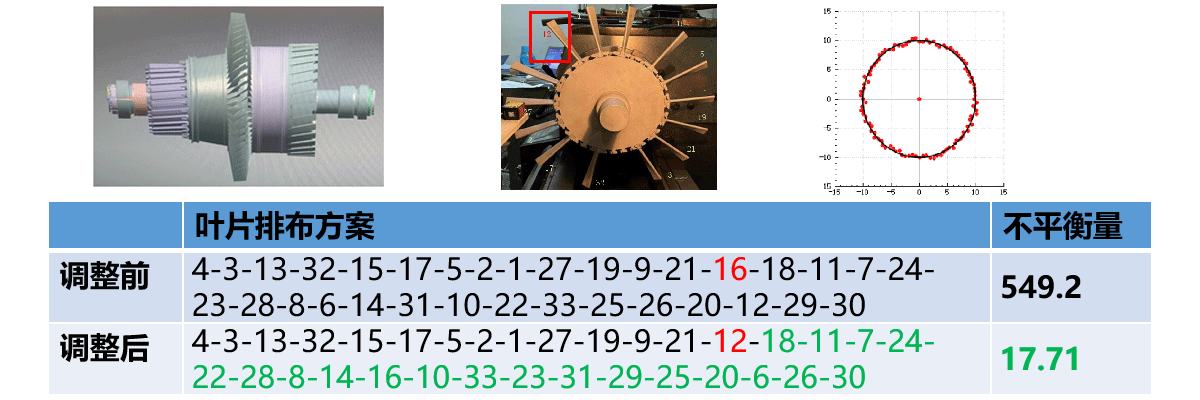
基于多层语义MBD的全周期数据集成孪生模型以零件设计为核心,包括工艺模型、检验模型、工艺规范、检验规范、工艺文件、加工过程数据、质量结果数据等,面向全流程制造的数据集,形成多层语义描述体系并以时空方式投影到三维模型,为每一个零件生成能够完整记录其加工状态的三维数字档案,实现零件加工全工艺流程的数字化、规范化,打通不同系统中的数据接口,使工艺工程师和现场操作人员更快捷方便可视化的获取零件全工艺流程数据,保证工艺固化,实现数据精准传递、快速查询、有效利用和快速追溯。基于多层语义MBD的全周期数据集成孪生模型可以有效支撑智能生产环境,并简化数字化与智能化生产各种软件与系统的复杂程度。
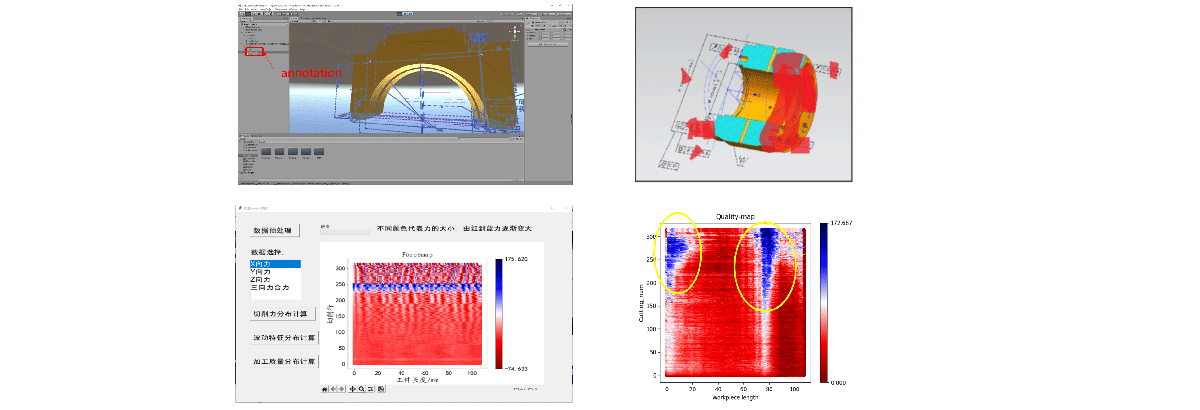
研究成果6:盘鼓装配中同轴度半实物仿真预测模型
一、二级盘鼓模拟件螺栓连接,螺栓数目8,在安装1号螺栓时,实际拧紧力矩为2.0N.m,同轴度预测9.865mm,对后续未安装的7颗螺栓的预紧力矩进行了优化,降低了同轴度偏差。
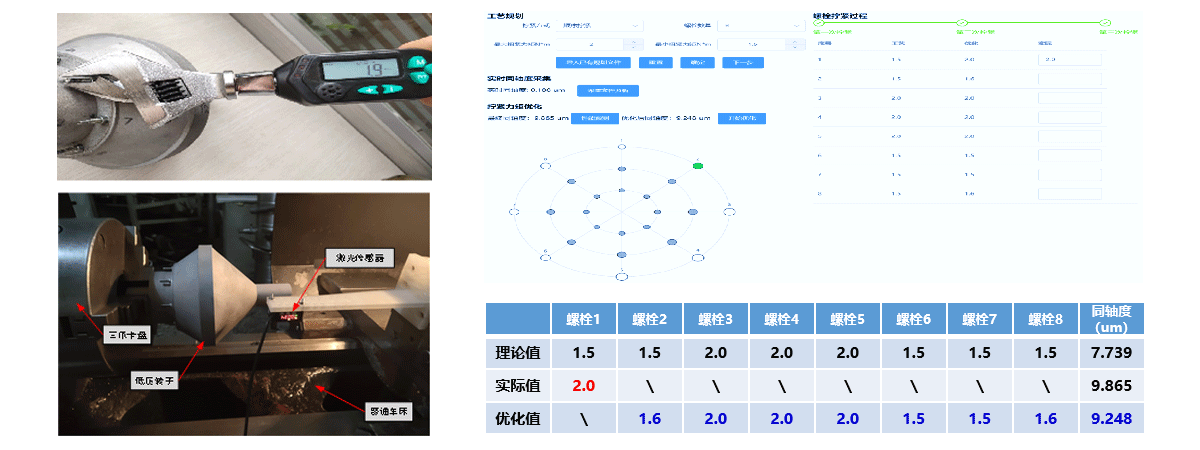
研究成果7:装配过程中产品性能演化预测
提出了机理与数据融合的产品性能半实物仿真预测方法,解决了装配过程中产品性能变化难以预测导致反复拆装问题,形成边装边调的新模式。
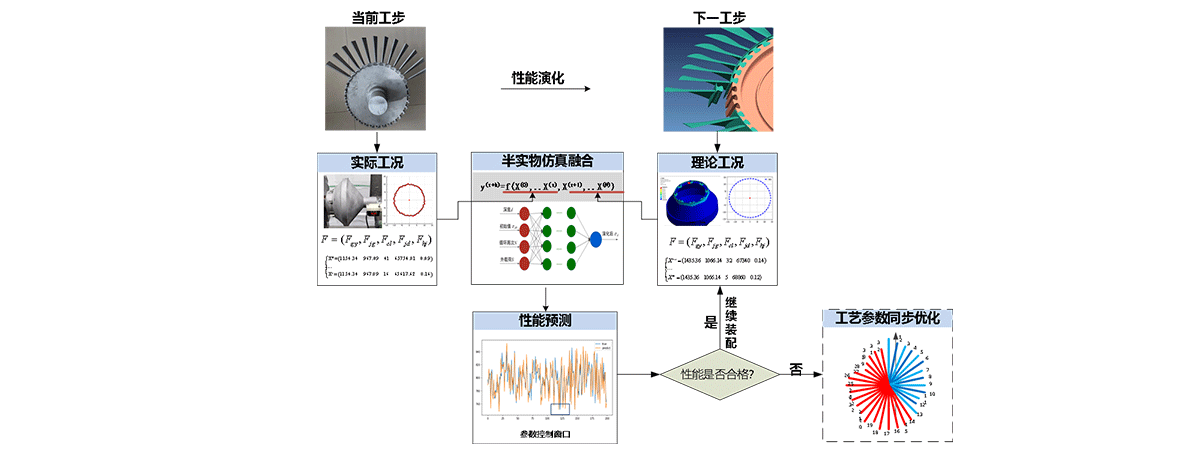
研究成果8:智能化系统
为实现系统运行过程智能化管控,针对系统内部资源、组件、部件等不同层级,结合人工智能、数字孪生、大数据分析等技术,联合研发形成可计算数字双胞胎平台、数字双胞胎监控系统、智能总控系统等智能化系统,从不同层次提高企业智能化水平,加速企业的智能化建设进度。
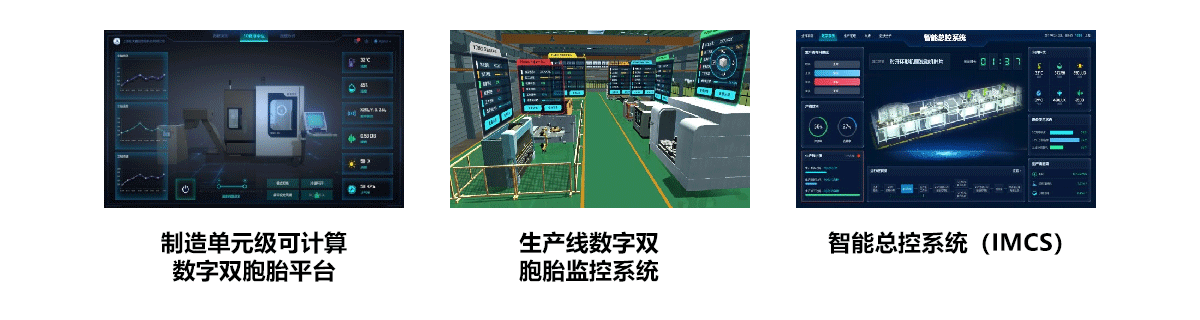
研究成果9:制造单元级可计算数字双胞胎平台
围绕五轴联动加工中心搭建加工过程可计算数字双胞胎平台,在对设备运行状态、加工状态实时感知的基础上,用于实时工况与系统能力、健康状态的实时监控、分析与预测,能够有效提高生产现场的局部智能化水平,助力企业实现智能制造。
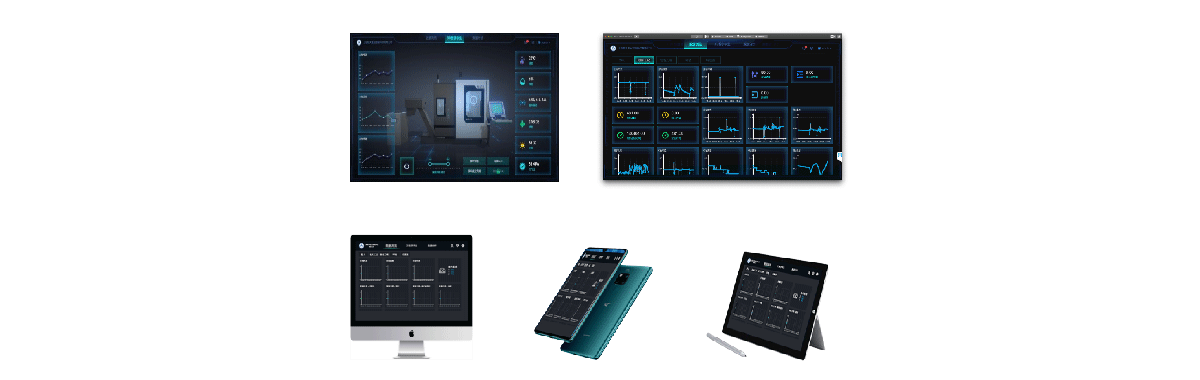