智能感知终端与系统研制
智能化感知终端产品
面向系统运行过程的全面感知需求,针对不同的场景,联合研发出不同系列的感知终端,实现环境、工况、性能、质量等内容的实时感知与动态分析,提高系统运行过程中的全面感知能力与智能化程度。
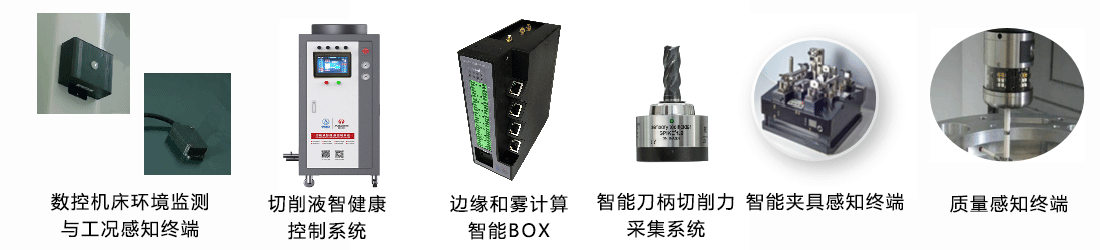
研究成果1:智能切削力感知系统
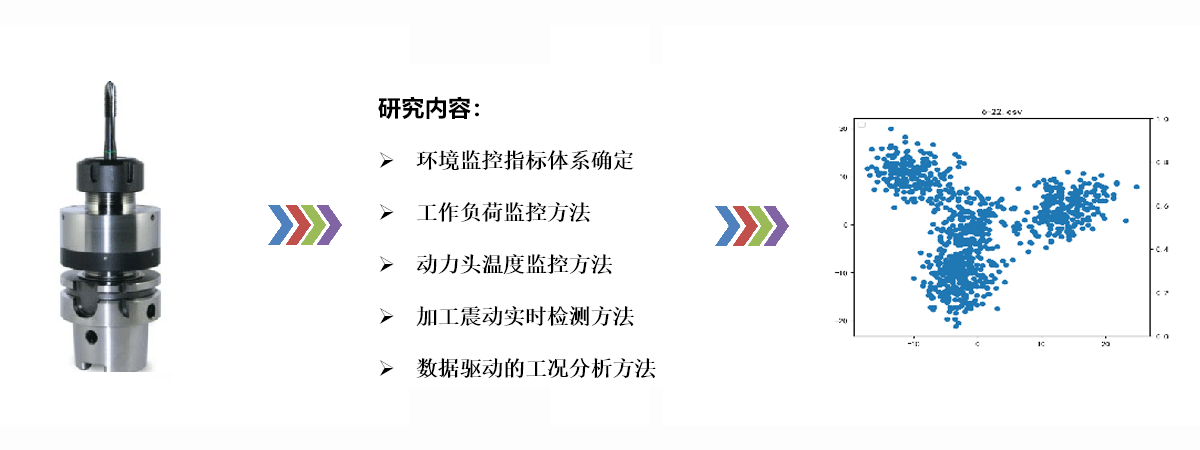
智能刀柄切削力系统
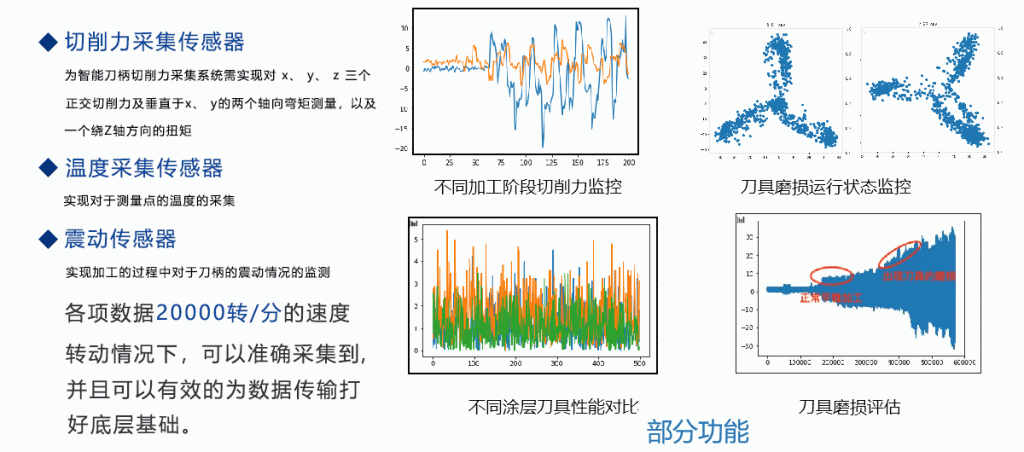
边缘和雾计算智能Box
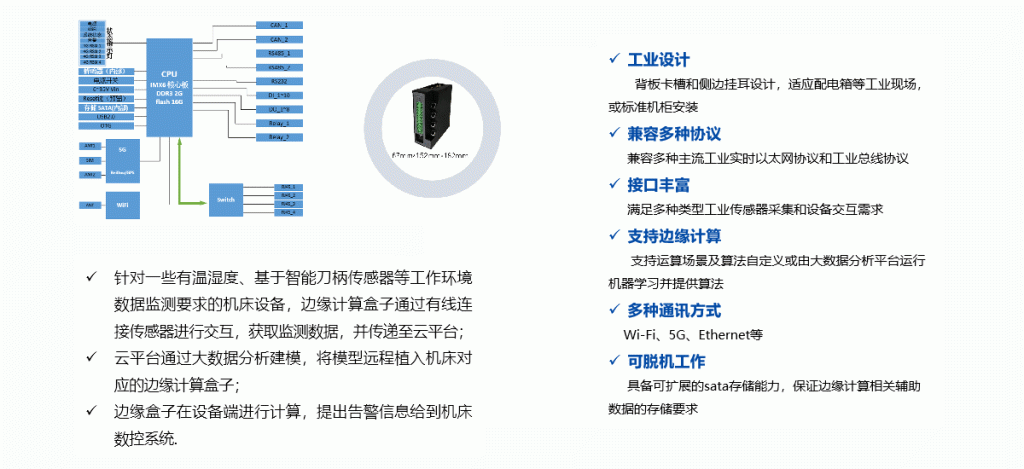
研究成果2:切削液健康控制系统
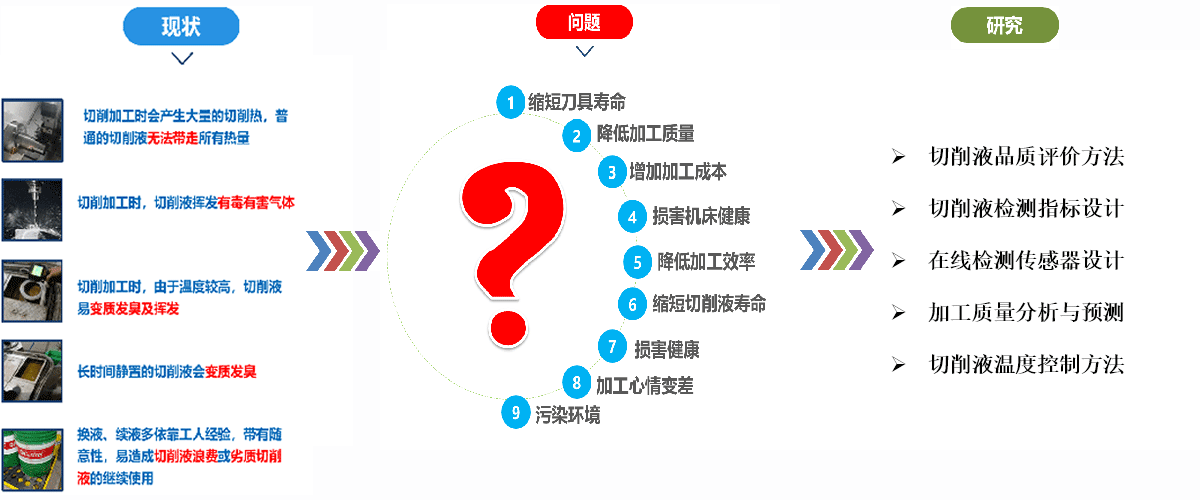
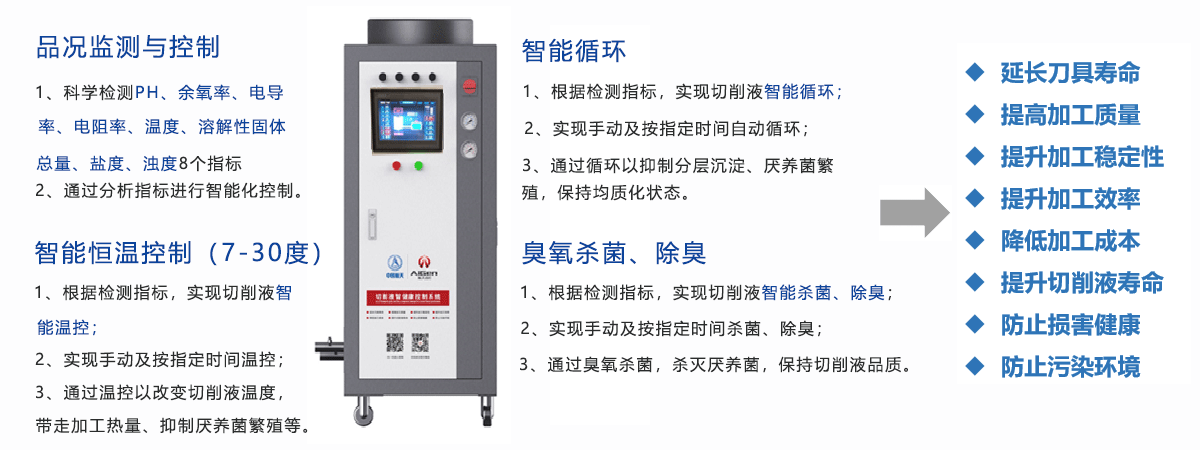
研究成果3:数控机床环境监控与工况感知系统
针对精密加工过程对数控机床环境动态变化监控的需求,研究数控机床所处声音、振动、粉尘、温度、光照、湿度等环境因素和工况的监控与分析方法,实现车间环境的动态感知。
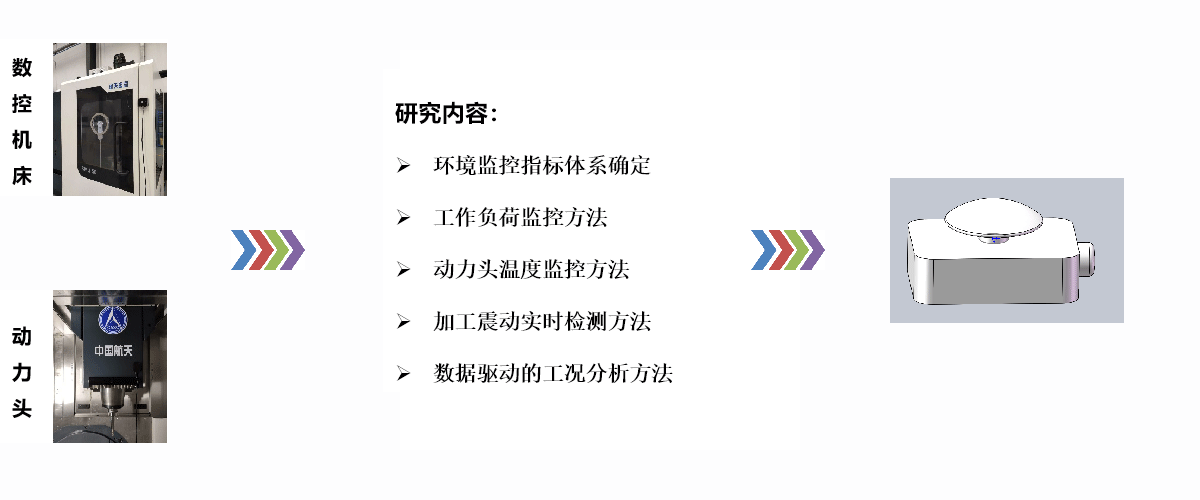
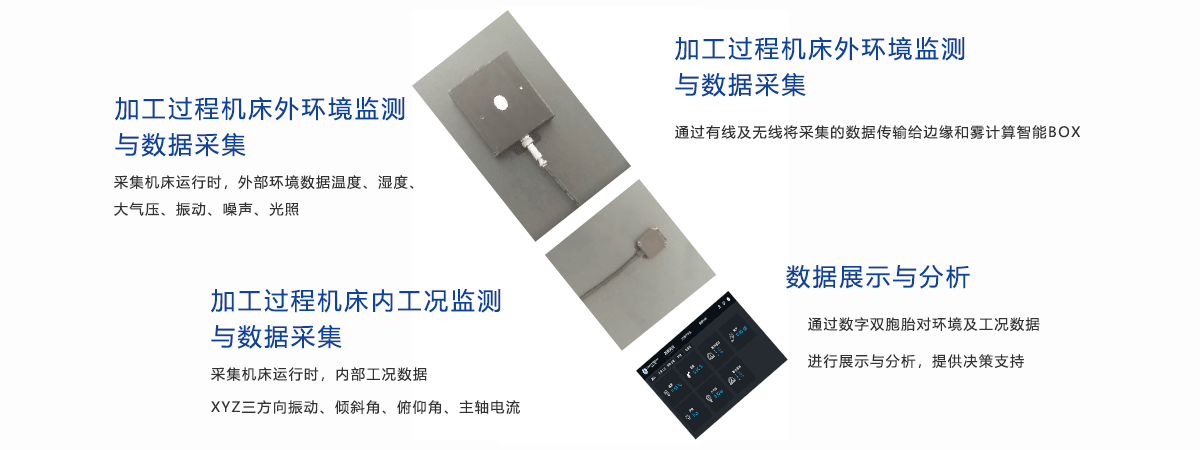
研究成果4:智能夹具感知终端
针对薄壁件加工场景下,研发可实时监测工件加工状态并依据状态反馈进行动态自行调整装夹状态的智能夹具。
加工过程中利用无线数据传输技术结合大数据分析对如切削参数、走刀路线、切削力、振动等的实时数据采集传输并分析,从而获得当前工况下工件加工状态反馈,进而装夹控制系统依据反馈结果采取相关措施,如夹紧力的大小变化、夹紧点位置的缩放等,最终达到控制偏移、减小加工变形及颤振的目的。
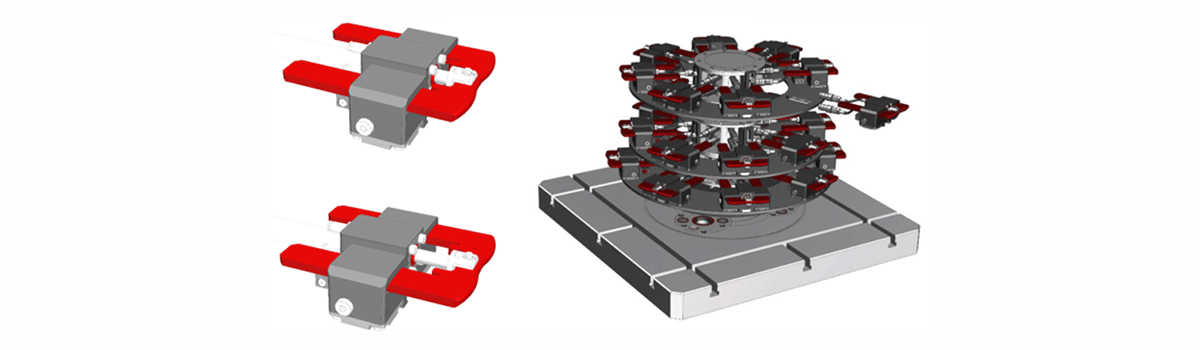
研究成果5:基于数据驱动的加工监测系统
针对各类加工场景下对监测数据进行客观感知的需求,研究基于极坐标的铣削加工弯矩数据可视化表达方法。
通过构建弯矩极坐标模型,带入由铣削数据中提取的信号特征,可视化出似于刀具刀刃的“刀花”图案。通过从极坐标图像的变化上反映出刀具相应齿的状态的变化,以便于在对铣削加工弯矩受力信号进行时序表达的同时,还能反应刀具磨损的情况,从而实现对弯矩数据所内涵的刀具状态更加清晰的物理意义刻画,也更方便用于人眼识别与计算机图形识别,对加工过程数据的异常进行诊断与分析。
将实时采集的加工数据与加工轨迹相结合,在三维空间中构建加工表面,并使用不同的色域进行标识,构建加工数据分布模型。通过分析、对比对数据分布云图,对加工状态、加工结果、加工表面质量等进行刻画,为后续预测等提供支撑。
针对零件的加工质量问题及早期失效常发生在应力集中部位的工程问题,开展切削过程中工件应力分布动态预测研究,为探究切削加工过程中的变形提供基础,进而达到保证产品加工质量的目的。
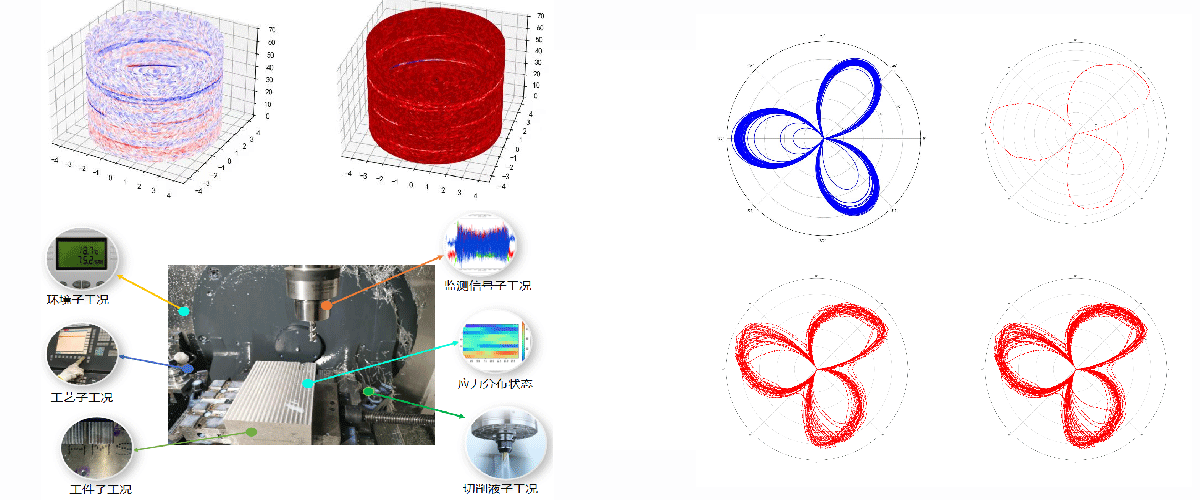
研究成果6:基于MBD技术的可视化质量检测引导系统
针对柴油机零部件可视化检验需求,结合现有的工艺流程与规范,开发形成基于MBD模型的可视化检测流程,集成在质量采集模块中,配合数字化量仪实现柴油机关重零部件可视化与数字化检测,在实现检验数据快速、准确录入、提高效率的同时,有效降低质量检测过程中错漏检。
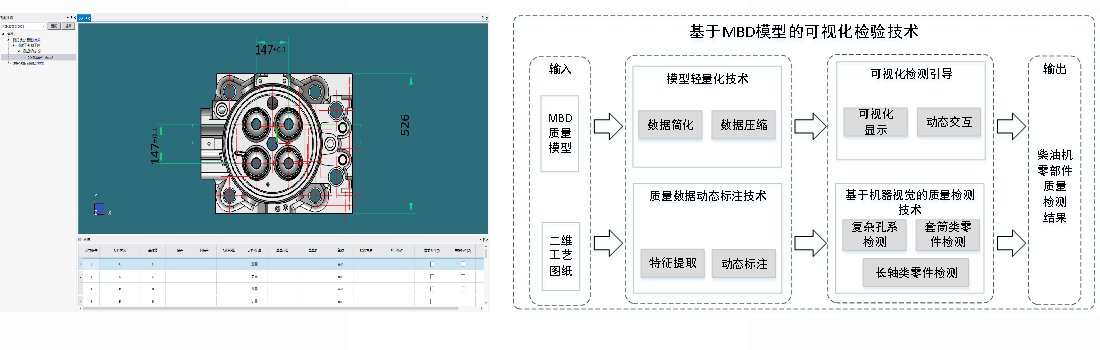